When making a purchasing decision, it’s important to consider more than just the upfront cost. You also need to think about the life cycle cost of the item in question. This is the total cost you will pay for owning and using the item over its lifetime. In this blog post, we will discuss what life cycle cost is and how to calculate it. We will also provide some tips for reducing your life cycle costs.
- What is the Life Cycle Cost?
- What is the life cycle costing process?
- What is life cycle cost analysis?
- How can we do the life cycle cost analysis?
- What are the limitations of Life cycle cost analysis?
- What are some tips for reducing your life cycle costs?
- 1. Choose durable & long-lasting products
- 2. Purchase reusable & recyclable products
- 3. Renting or borrowing
- 4. Renewable energy projects
- What is the life cycle cost of a building?
- What is capital budgeting?
- Research and development (RD)
- Investment costs
- Operating costs
- Decommissioning and clean-up costs
- Conclusion
- FAQs
- What is the basic formula of a life cycle cost?
- What factors are included in the net present value?
- What are some examples of building systems that can be analyzed using life cycle cost analysis?
- How do you determine the discount rate for a life cycle cost analysis?
- What are the different types of costs that can make or break a project?
- What is PV residual value?
What is the Life Cycle Cost?
When making a major purchase, it’s important to consider the total cost of ownership or life cycle cost. This includes not only the initial price but also the costs of operating and maintaining the item over its lifetime. For example, a car with a low purchase price might require more expensive repairs, while a more expensive car might have lower fuel and insurance costs.
To calculate life cycle cost, you’ll need to estimate the cost of ownership for each alternative and then compare the results. The key factors to consider are the initial purchase price, depreciation, fuel costs, insurance premiums, maintenance and repair expenses, and resale value. By taking all of these factors into account, you can make a more informed decision about which product is the best value for your needs.
What is the life cycle costing process?
What is the life cycle costing? Life cycle costing is the process of calculating the total costs of owning and operating an asset over its entire life. This includes the initial cost, as well as the costs of operation and maintenance. By taking into account all these costs, businesses can make more informed decisions about which assets to invest in.
Calculating life cycle costs is not always simple, but there are various methods that can be used. The most important factors to consider are the overall costs, including both monetary and non-monetary costs, and the economic life of the asset. In some cases, it may also be necessary to account for inflation. Once all these factors have been considered, businesses can make decisions based on which option will provide the best value over the long term.
Although life cycle costing can be complex, it is a valuable tool for businesses to use when making investment decisions. By taking into consideration all the costs associated with an asset, companies can ensure that they are making the best possible decision for their needs.
What is life cycle cost analysis?
Life cycle cost analysis (LCCA) is a method of economic appraisal that includes all costs and benefits associated with a project over its entire life span. This includes the initial investment cost, ongoing operating costs, maintenance costs, and disposal or recycling costs.
Life cycle cost analysis can be used to compare different options for a project, and it is often used in conjunction with an environmental impact assessment to ensure that the most sustainable option is selected. While Life cycle cost analysis can be a complex process, it is an essential tool for making sound economic decisions about long-term projects.
How can we do the life cycle cost analysis?
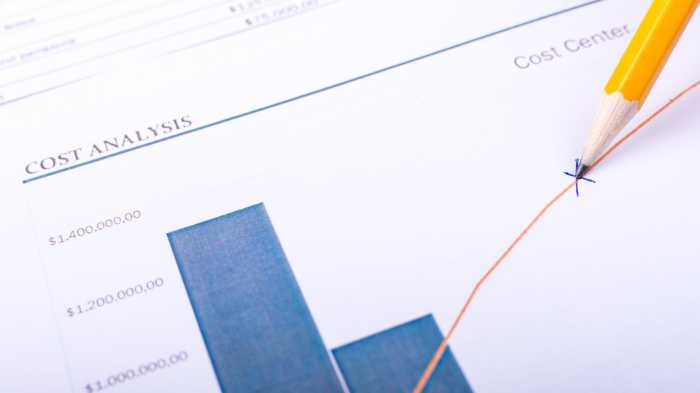
There are many ways to calculate the Life cycle cost analysis, but the most important factor is to consider all costs associated with the product or system over its lifetime. With this information in hand, businesses and consumers can make more informed decisions about which products or systems offer the best value. To accurately calculate the Life cycle cost analysis, businesses need to consider all direct and indirect costs associated with a product or system.
This includes not only the purchase price of the item but also installation costs, shipping and handling charges, repairs and maintenance costs, and energy consumption. In addition, businesses need to account for any expected changes in these costs over time. By considering all of these factors, businesses can get a more accurate picture of the true cost of a product or system and make better decisions about which products or systems offer the best value.
What are the limitations of Life cycle cost analysis?
As with any tool, there are certain limitations to the Life cycle cost analysis. For example, the Life cycle cost analysis does not take into account intangible factors such as customer satisfaction or brand loyalty.
In addition, the Life cycle cost analysis is based on assumptions about the future, such as how long the product or system will be used and how much it will cost to maintain over time.
Despite these limitations, the Life cycle cost analysis remains a valuable tool for businesses and consumers who want to make informed decisions about their purchasing choices.
What are some tips for reducing your life cycle costs?
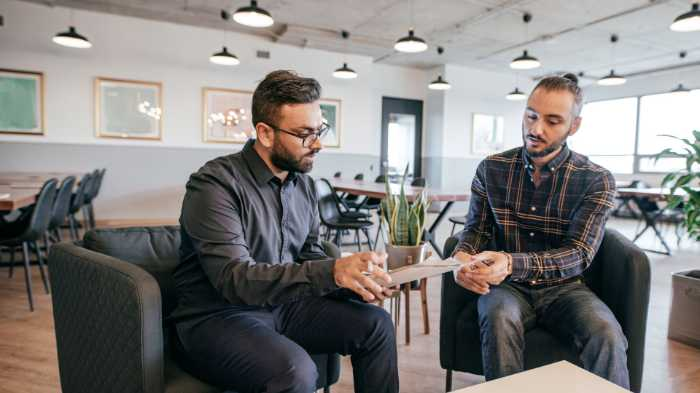
Any product, from a piece of clothing to a car, has a life cycle that includes the costs of manufacture, use, and disposal. To reduce your life cycle costs, it’s important to consider the entire span of a product’s life, from its creation to its eventual end.
1. Choose durable & long-lasting products
One way to do this is to choose products that are durable and long-lasting. Items made with quality materials and construction will cost more upfront, but they will save you money in the long run by needing fewer repairs and replacements.
2. Purchase reusable & recyclable products
Another way to reduce your life cycle costs is to purchase items that can be reused or recycled. This includes everything from clothes to electronics. Not only does this reduce waste, but it also saves you money by eliminating the need to buy new products.
3. Renting or borrowing
Finally, you can save money by renting or borrowing items instead of purchasing them outright. This is particularly effective for items that are only used occasionally, such as tools or party supplies.
4. Renewable energy projects
You can also save money over the long term by investing in renewable energy projects. These include solar panels, wind turbines, and geothermal systems. While the initial costs may be higher than traditional energy sources, renewable energy is free once it’s installed and can significantly reduce your life cycle costs providing cost-effectiveness and net savings. Moreover, energy and water conservation can also reduce operation and maintenance costs by a margin.
You can’t improve what you don’t measure.
Free Verified Carbon Calculators.
Erase Your Carbon Footprint in less than 5 Minutes
Personal Carbon Footprint Calculator
Business Carbon Footprint Calculator
What is the life cycle cost of a building?
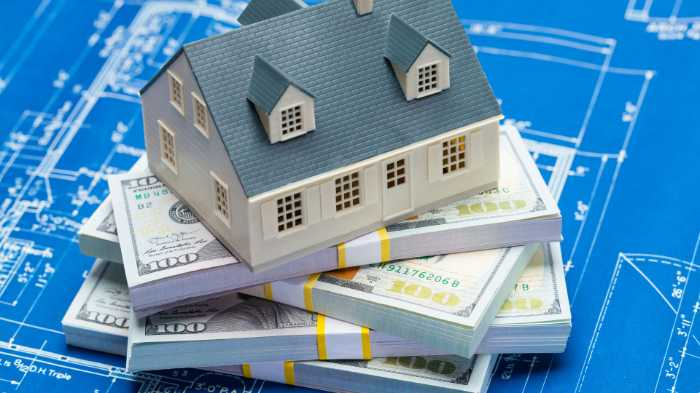
The life cycle cost of a building refers to the total cost of ownership over the course of its lifespan. This includes costs related to construction, operation, maintenance, and decommissioning. To calculate the life cycle cost of a building, all of these expenses must be considered. For example, the initial construction cost may include the cost of materials, labor, permits, and inspections.
Operating costs may include utility bills, repairs and maintenance, and insurance. When all of these costs are added up, they can give a clear picture of the true cost of owning a building. Life cycle costing is an important tool for making informed decisions about which buildings to construct and how to best maintain them. By taking all costs into account, life cycle cost calculation can help to ensure that buildings are built and maintained in a way that is economically efficient and environmentally sustainable. Moreover, life cycle costing can also determine the savings-to-investment ratio through initial costs or the total life cycle cost.
What is capital budgeting?
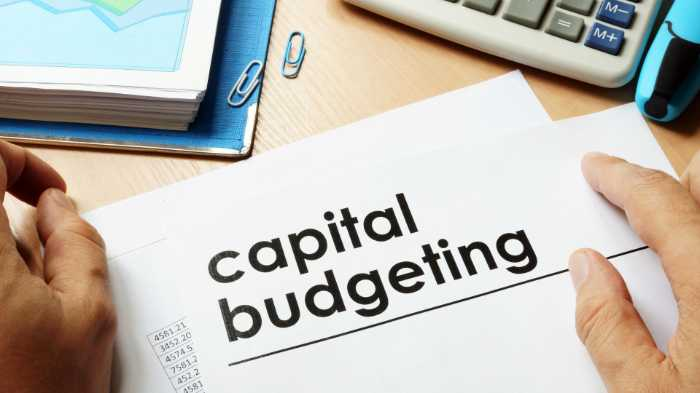
Capital budgeting is the process of evaluating and selecting long-term investments for a company. These investments typically have a life of more than one year and can include anything from new machinery to factory expansion. Capital budgeting decisions can have a major impact on a company’s profitability and growth, so it is crucial to carefully consider all options before making a decision.
There are several different methods that can be used to evaluate investment opportunities, such as net present value and internal rate of return. Ultimately, the goal of capital budgeting is to choose investments that will maximize shareholder value.
There are four major costs that impact capital budgeting:
Research and development (RD)
Research and development (RD) cost refers to the expenses incurred by a company during the process of creating new products or services. This includes costs associated with research, design, prototyping, testing, and marketing. RD costs can be high, and they are often considered sunk costs, which means that they cannot be recovered once incurred.
For this reason, companies must carefully consider RD costs before making investment decisions. In some cases, RD costs may be tax-deductible, which can help to offset some of the expenses. Overall, RD cost is an important factor to consider when making business decisions.
Investment costs
Investment costs are a necessary part of doing business, but they can also be a significant expense. Investment costs are incurred when a company makes an actual investment, such as buying new machinery. These costs can be high, but they usually result in some immediate benefits.
For example, the new machinery may increase production capacity or allow for a higher level of quality control. In some cases, the investment may also lead to increased employee morale and motivation. While investment costs can be substantial, companies need to weigh the potential benefits against the risks. Careful planning and analysis can help to ensure that investments are made wisely and provide the desired results.
Operating costs
Operating costs are the costs associated with running a business on a day-to-day basis. This includes things like utilities, rent, payroll, and supplies. For most businesses, operating costs are the largest expense they will incur. As such, it is important for businesses to carefully track their operating costs and find ways to reduce them where possible.
Decommissioning and clean-up costs
Decommissioning and clean-up costs are incurred when a project comes to an end. These costs can be high, but they are often worth it to preserve the integrity of the site and avoid environmental damage. The process of decommissioning involves removing all structures and materials that are no longer needed, as well as decontaminating the area to make it safe for future use.
Once the site is clear, it must be cleaned up and restored to its original condition. This process can be costly, but it is essential to protect the environment and ensure the safety of those who will use the site in the future.
Conclusion
The life cycle cost of a product is the total cost of ownership over its entire lifetime. This includes the initial purchase price, operating costs, maintenance costs, and disposal costs. Calculating the life cycle cost can help you make informed decisions about which products to buy and how to use them. For example, a product with a low initial purchase price but high operating costs may have a higher life cycle cost than a product with a higher initial purchase price but lower operating costs. Likewise, a product with a long lifespan may have a lower life cycle cost than a product with a shorter lifespan. By taking the time to calculate the life cycle cost of a product, you can save money in the long run.
FAQs
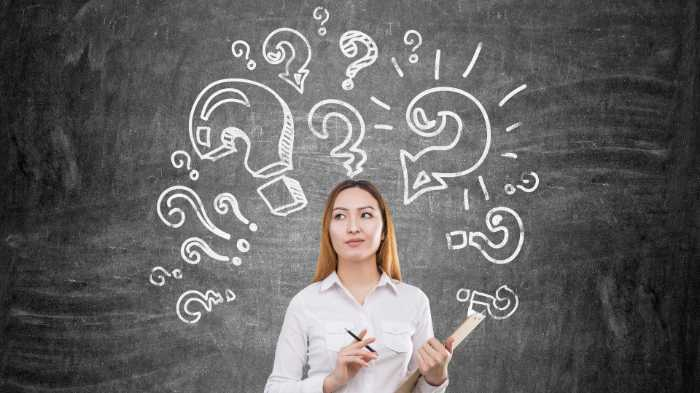
What is the basic formula of a life cycle cost?
The basic formula for life cycle cost is Net Present Value or Capital cost + Operating Costs + Maintenance Costs + Replacement Costs – residual value.
What factors are included in the net present value?
The net present value includes all the costs, including the initial cost of the asset, the interest rate, and the expected number of years the asset will be used.
What are some examples of building systems that can be analyzed using life cycle cost analysis?
Some examples of building systems that can be analyzed using life cycle cost analysis include HVAC systems, lighting systems, and security systems. The expected useful life of a typical building system is 20-30 years.
How do you determine the discount rate for a life cycle cost analysis?
The discount rate for a life cycle cost analysis is typically determined by the project’s funding source. For example, federal projects typically use a discount rate of 2.5%.
What are the different types of costs that can make or break a project?
There are several types of costs that can impact a project: initial cost, total cost, maintenance and repair costs, replacement costs, energy costs, operational costs, additional costs, less disposal costs, financing costs, operating costs, disposal costs, and environmental costs. Some of these may be more relevant than others, depending on the project. For example, if you’re considering a home renovation, energy costs may not be as big of a factor as they would be in a commercial building project. It’s important to consider all potential cost factors when planning a project to ensure its success.
What is PV residual value?
PV (photovoltaic) residual value is the percentage of a PV system’s original cost that will be recovered when the system is sold at the end of its useful life. In other words, it’s a measure of how much value a PV system retains over time. The useful life of a PV system is typically 20-25 years, so the residual value at the end of that period would be 20-25% of the original cost. However, PV systems can often last much longer than that, so the actual residual value may be higher. Factors that will affect the PV residual value include its age, its efficiency, and the current market conditions for used PV systems.

Dean Emerick is a curator on sustainability issues with ESG The Report, an online resource for SMEs and Investment professionals focusing on ESG principles. Their primary goal is to help middle-market companies automate Impact Reporting with ESG Software. Leveraging the power of AI, machine learning, and AWS to transition to a sustainable business model. Serving clients in the United States, Canada, UK, Europe, and the global community. If you want to get started, don’t forget to Get the Checklist! ✅